Fresh from bringing its expertise to the newly-opened Mandarin Oriental Mayfair, furniture design and manufacturing company Hospitality Projects lifts the lid on its process, growth and milestone projects.
Founded in 2017 as part of the WI International Group, Hospitality Projects began with a bold vision to transform bespoke furniture design. What started as a small consultancy in London quickly evolved into a major player in the industry. By 2020, the brand opened its own workshop, marking a significant leap from outsourcing to in-house manufacturing.
The company expanded its operations by investing in a state-of-the-art 52,000ft² facility in 2021. This strategic move allowed Hospitality Projects to adapt and thrive during challenging times, leading the company to where it stands today – as a leader in the hospitality furniture industry.
Synergy, Excellence and Craftsmanship: The Design and Manufacturing Process
Since its inception, Hospitality Projects has integrated all aspects of design and manufacturing under one roof. This vertical integration – spanning upholstery, woodwork, joinery and finishing – allows for greater control over quality, timelines and customisation. Every piece of furniture is the result of close collaboration between departments, ensuring meticulous craftsmanship and attention to detail throughout the entire process.
All Senior Project Managers are deeply involved, guiding each project through in-depth consultations, careful material selection and shop drawing phases. Advanced technologies like computer-aided design and sustainable practices ensure that each project is both functional and aesthetically refined. As Senior Project Manager Natasha Hubbard puts it: “When you think about creating something, you always have to think about processes: ‘How do I take this idea and actually get it built?'”
Sourcing: More Than Just Materials
Hospitality Projects is committed to sourcing materials from independent local businesses, fostering strong connections with artisans and craftspeople while maintaining a sustainable manufacturing approach.
The focus extends beyond simply acquiring materials; each grain and texture reflects a story of collaboration within the artisanal community. By integrating these elements into their designs, clients are able to infuse their spaces with personal meaning and significance, creating environments that are rich with authenticity and character.
Seamless Integration of Craftsmanship
Once sourced, these materials move through Hospitality Projects’ three core manufacturing units. In Unit 1: Timber Workshop, precise CNC machining ensures solid foundations. Unit 2: Spray Shop applies custom finishes that enhance each piece’s aesthetic. Finally, in Unit 3: Upholstery Workshop, expert upholsterers complete the transformation, adding the finishing touches that bring each design to life.
This synergy across units results in bespoke, high-quality furniture with a story behind every detail.
Overcoming Industry Challenges: Reducing the Burden on Clients
In an industry where tight deadlines, fluctuating material costs and ever-changing client expectations are the norm, Hospitality Projects actively works to alleviate these pressures. The company streamlines operations, maintains strong supplier relationships and manages every aspect of design, production and finishing in-house. This integrated approach ensures reliability, flexibility and consistent quality, offering clients peace of mind and helping projects stay on schedule and within budget.
Prestigious Collaborations
Hospitality Projects has had the privilege of partnering with a wide range of renowned brands. For Soho House Stockholm, the company crafted over 200 unique pieces, while at Nobu Hotel Shoreditch, it designed more than 80 custom items. The most recent achievement was producing over 3,500 bespoke pieces for Mandarin Oriental Mayfair, further solidifying Hospitality Projects’ leadership in the hospitality furniture industry.
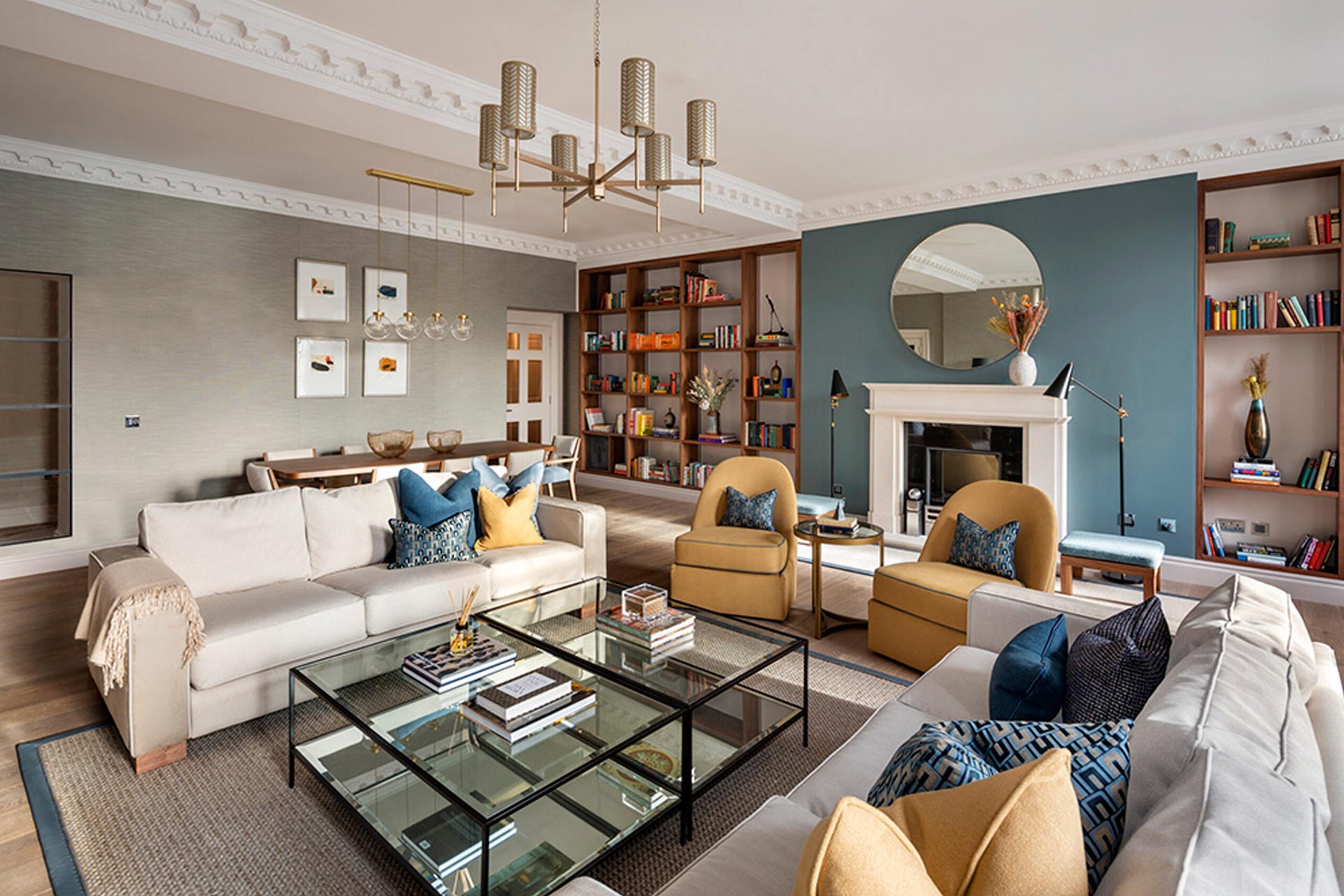
Related Posts
3 October 2024
W Hotels unveils reimagined West Coast flagship
2 October 2024